Understanding Production SLA: The Key to Successful Business Operations
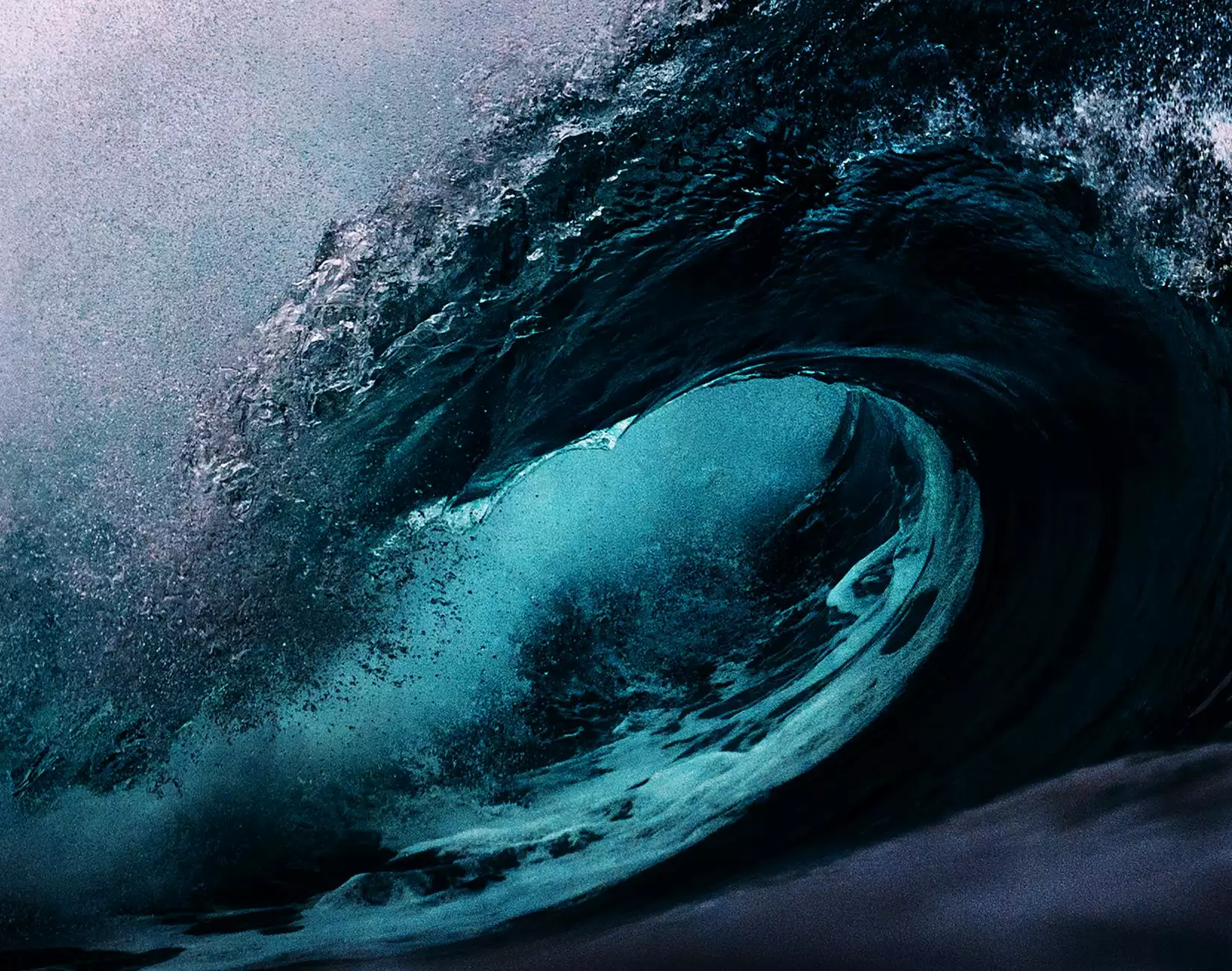
In the fast-paced world of business, production SLA plays a pivotal role in ensuring that organizations operate efficiently and effectively. A Service Level Agreement (SLA) in the context of production has become an essential tool for managing performance standards, expectations, and quality in various industries, particularly in Art Supplies, Product Design, and 3D Printing. This article delves into the intricacies of production SLA, its importance, and best practices for implementation to achieve outstanding results and maintain a competitive edge.
What is Production SLA?
A Production SLA is a formal contract between a service provider and a customer that specifies, among other things, the expected level of service or performance concerning production outputs. This agreement outlines measurable metrics and standards that the supplier must guarantee while providing services related to production.
Key Components of Production SLA
Understanding the components of a production SLA is essential for businesses looking to optimize their operations. Here are some key elements typically included:
- Service Description: Clearly define what services are being provided. This includes details of the production processes involved.
- Performance Metrics: Include quantitative and qualitative metrics that gauge service performance, such as timeliness, quality, and efficiency.
- Responsibilities: Outline specific responsibilities of both parties to avoid any ambiguities in service delivery.
- Monitoring and Reporting: Define how performance will be monitored and reported, including frequency and methods of communication.
- Penalties and Remedies: Establish consequences for failing to meet the agreed standards, including penalties, remedies, and escalation procedures.
The Importance of Production SLA in Business
Integrating a robust production SLA into business operations offers numerous advantages:
1. Enhanced Efficiency
By clearly outlining expectations and responsibilities, a production SLA enhances operational efficiency. Organizations can streamline processes and focus on achieving key performance indicators (KPIs) that directly impact productivity.
2. Improved Quality Assurance
Production SLAs help maintain high standards of quality. With clear metrics in place, businesses can ensure that production outputs meet specified requirements, thus minimizing defects and ensuring customer satisfaction.
3. Mitigation of Risks
By defining responsibilities and performance standards in the SLA, businesses can effectively mitigate risks associated with production failures. This reduces the likelihood of disputes and enhances trust between service providers and clients.
4. Easier Communication
With a production SLA, communication becomes more straightforward. Both parties understand what is expected and how performance will be monitored, facilitating transparent interactions and enhancing collaboration.
Applying Production SLA in Various Industries
Art Supplies
In the art supplies industry, production SLAs can assure clients that their materials are delivered on time and meet specific quality standards. Whether it's ensuring that paints arrive without defects or that canvases are of the highest quality, a well-defined SLA ensures that the production processes roll out smoothly, aligning with the creative needs of artists.
Product Design
For businesses in product design, SLAs are critical in synchronizing design outputs with production capabilities. Designers can set timelines and quality expectations while manufacturers commit to maintaining those standards. This synergy enhances the workflow, reduces redesign times, and ensures products reach the market faster.
3D Printing
The realm of 3D printing particularly benefits from SLAs due to the technology's complexity and rapid evolution. In creating prototypes or final products, ensuring that specifications are met is vital. Production SLAs help manage client expectations, often leading to faster turnaround times and higher satisfaction rates as deliverables align with desired outcomes.
Developing an Effective Production SLA
Creating a production SLA requires careful consideration and strategic planning. Here are steps to establish an effective SLA:
1. Understand Your Needs
Begin by thoroughly understanding your business needs and the specific services being provided. Identify key metrics that align with your operational and customer satisfaction goals.
2. Engage Stakeholders
Involve key stakeholders from both the service provider and customer sides in drafting the SLA. This collaborative approach ensures that the agreement meets the needs and expectations of everyone involved.
3. Define Clear Metrics
Clearly define measurable metrics that will gauge performance and ensure they are achievable and relevant. This makes it easier to monitor compliance with the SLA.
4. Regular Reviews
SLAs should not be static documents. Schedule regular reviews to assess performance against the SLA and make adjustments as needed to account for changes in business needs or market conditions.
5. Training and Resources
Ensure that everyone involved in the execution of the SLA is adequately trained and understands their responsibilities. Providing necessary resources and support will lead to better compliance and satisfaction.
Challenges in Implementing Production SLA
While production SLAs offer significant benefits, challenges can arise during implementation. Here are some common obstacles:
1. Measuring Performance Accurately
Establishing reliable and accurate metrics can be difficult. Businesses must invest in tracking and reporting tools to gather the necessary data effectively.
2. Complexity of Services
In industries such as 3D printing and product design, the complexity of services may make it challenging to define clear SLAs. Service providers must ensure that agreements encompass all facets of the services offered.
3. Changing Business Needs
As companies evolve, their operational needs may also change. Keeping SLAs aligned with changing business dynamics is crucial for continued relevance and efficacy.
Best Practices for Managing Production SLAs
To maximize the effectiveness of production SLAs, consider the following best practices:
- Maintain Transparency: Foster a culture of open communication regarding performance expectations and results. This reduces misunderstandings and encourages collaboration.
- Utilize Technology: Leverage technology solutions to monitor compliance with performance metrics. This can enhance accuracy and accessibility of performance data.
- Encourage Feedback: Regularly solicit feedback from all stakeholders to identify issues or areas for improvement. This promotes continual enhancement of service delivery.
- Adapt and Evolve: Be willing to revisit and adjust SLAs based on feedback, performance data, and changing market demands.
Conclusion
The significance of a well-structured production SLA cannot be overstated. In an era where operational excellence is essential for business sustainability, SLAs serve as guiding frameworks that enhance efficiency, improve quality, and foster fruitful partnerships between businesses and their service providers. By understanding the intricacies of production SLAs and applying best practices within the Art Supplies, Product Design, and 3D Printing sectors, companies can navigate the complexities of modern production landscapes while ensuring satisfaction for their clients.
In summary, implementing a production SLA is not merely a compliance necessity but a strategic move that empowers businesses to thrive in competitive environments. By adhering to the insights and tips outlined in this article, organizations can establish robust SLAs that drive success and foster long-lasting relationships.